Porosity in Welding: Identifying Common Issues and Implementing Ideal Practices for Avoidance
Porosity in welding is a prevalent problem that usually goes undetected until it creates considerable issues with the honesty of welds. This usual problem can endanger the toughness and toughness of bonded structures, positioning security dangers and resulting in expensive rework. By understanding the origin triggers of porosity and executing reliable prevention strategies, welders can dramatically enhance the quality and integrity of their welds. In this conversation, we will explore the essential factors adding to porosity formation, analyze its damaging impacts on weld performance, and review the very best practices that can be embraced to minimize porosity incident in welding procedures.
Typical Sources Of Porosity

One more frequent offender behind porosity is the presence of contaminants on the surface of the base metal, such as oil, grease, or corrosion. When these impurities are not properly gotten rid of before welding, they can vaporize and become caught in the weld, triggering problems. Additionally, using unclean or damp filler products can introduce impurities into the weld, adding to porosity concerns. To reduce these common root causes of porosity, detailed cleansing of base metals, proper securing gas choice, and adherence to optimum welding criteria are crucial techniques in attaining high-quality, porosity-free welds.
Effect of Porosity on Weld High Quality

The visibility of porosity in welding can substantially compromise the architectural honesty and mechanical residential or commercial properties of bonded joints. Porosity develops gaps within the weld metal, compromising its general toughness and load-bearing ability.
Welds with high porosity degrees often tend to exhibit lower influence toughness and decreased ability to deform plastically before fracturing. Porosity can hamper the weld's ability to effectively send pressures, leading to early weld failure and potential safety and security threats in important frameworks.
Best Practices for Porosity Avoidance
To boost the structural integrity and top quality of welded joints, what specific actions can be executed to minimize the event of porosity during the welding procedure? Porosity avoidance in welding is essential to ensure the honesty and strength of the last weld. One effective technique is appropriate cleansing of the base metal, getting rid of any type of contaminants such as corrosion, oil, paint, or moisture that can result in gas entrapment. Ensuring that the welding devices is in great problem, with clean consumables and ideal gas flow rates, can additionally considerably lower porosity. Furthermore, keeping a stable arc and regulating the more information welding parameters, such as voltage, present, and take a trip speed, aids create a constant weld swimming pool that lessens the risk of gas entrapment. Utilizing the proper welding technique for the certain product being welded, such as changing the welding angle and weapon position, can additionally protect against porosity. Regular assessment of welds and prompt removal of any kind of issues determined throughout the welding procedure are important methods to stop porosity and produce premium welds.
Value of Correct Welding Strategies
Applying appropriate welding techniques is vital in guaranteeing the architectural integrity and top quality of welded joints, building upon the structure of effective porosity avoidance steps. Too much heat can lead to boosted porosity due to the entrapment of gases in the weld pool. Furthermore, using the proper welding parameters, such as voltage, current, and take a trip speed, is critical for accomplishing audio welds with minimal porosity.
Moreover, the selection of welding process, whether it be MIG, TIG, or stick welding, must straighten with the particular demands of the task to guarantee ideal results. Correct cleaning and preparation of the base steel, along with selecting the best filler product, are additionally important elements of proficient welding methods. By sticking to these ideal techniques, welders can reduce the threat of porosity development and produce premium, structurally audio welds.
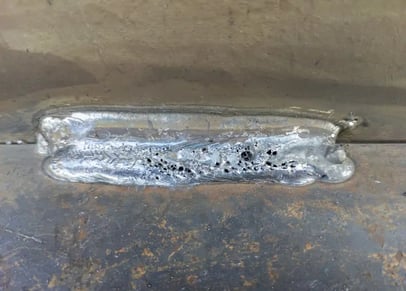
Testing and High Quality Control Procedures
Quality assurance measures play an essential role in verifying the stability and integrity of bonded joints. Examining treatments are important to detect and prevent porosity in welding, ensuring the toughness and toughness of the final product. Non-destructive screening approaches such as ultrasonic screening, radiographic screening, and visual examination are commonly employed to identify potential problems like porosity. These techniques enable the assessment of weld quality without compromising the stability of the joint. What is Porosity.
Post-weld examinations, on the other hand, examine the last weld for any flaws, consisting of porosity, and confirm that it meets defined criteria. Executing a detailed top quality control plan that includes complete screening procedures and assessments is critical to reducing porosity problems and guaranteeing the total high quality of welded joints.
Final Thought
Finally, porosity in welding can find more be a common problem that impacts the top quality of welds. By recognizing the usual reasons for porosity pop over to these guys and implementing best methods for avoidance, such as appropriate welding techniques and screening measures, welders can ensure excellent quality and dependable welds. It is necessary to focus on prevention techniques to reduce the incident of porosity and preserve the stability of welded structures.
Comments on “What is Porosity in Welding: Finest Practices for Preventing Porous Welds”