The Vital Function of Tank Welding Inspection in Ensuring Structural Honesty and Security Conformity in Industrial Applications
In the realm of commercial applications, container welding examination emerges as a crucial aspect in protecting architectural integrity and making sure conformity with safety laws. Utilizing a combination of methods such as aesthetic assessments and advanced testing approaches, these assessments offer to identify and alleviate possible flaws before they intensify into considerable risks.
Relevance of Container Welding Assessment
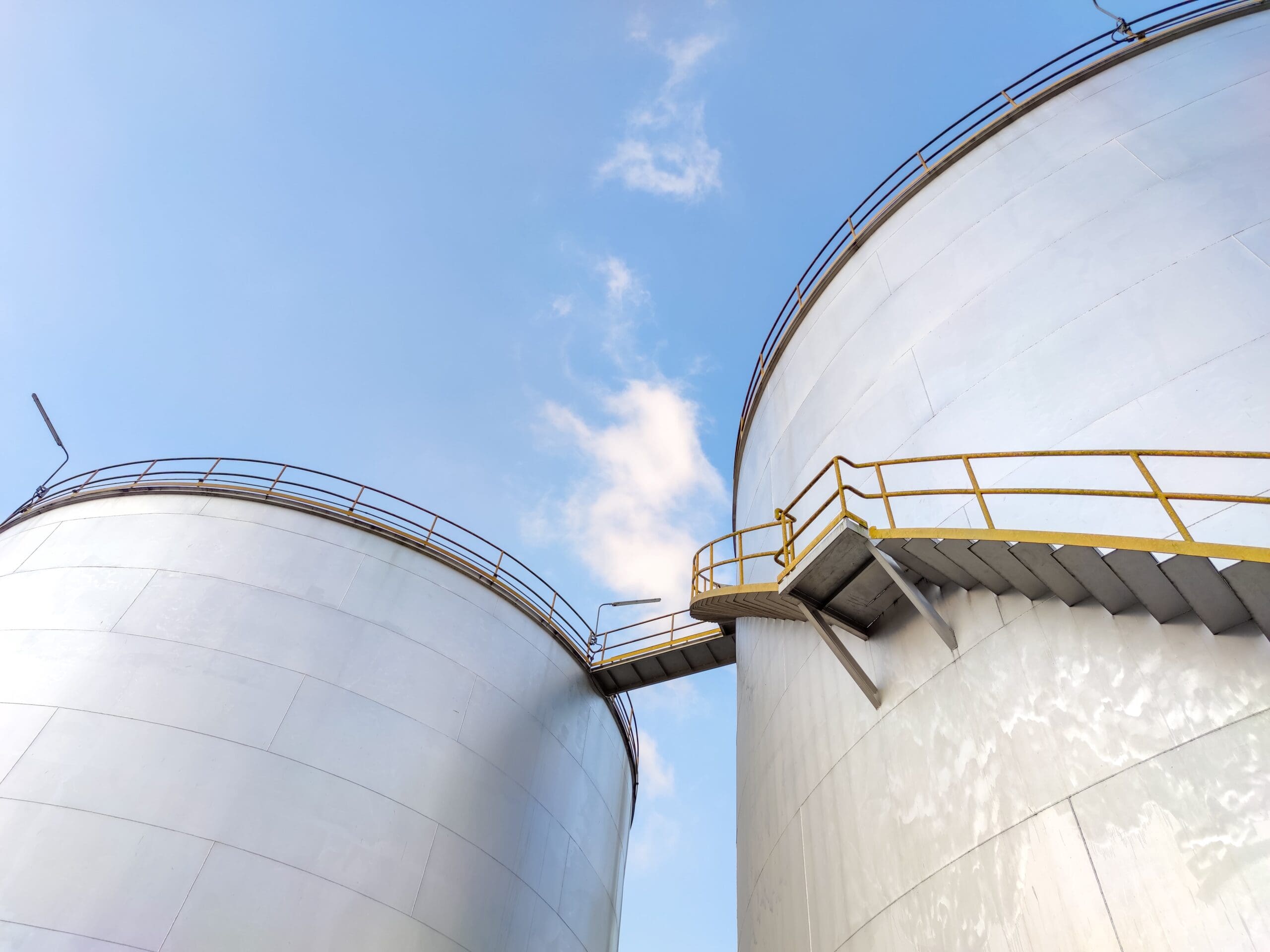
Making sure compliance with industry criteria and laws is an additional considerable aspect of tank welding examination. Regulative bodies mandate stringent guidelines for the construction and upkeep of tank, and comprehensive assessments aid companies abide by these needs. Non-compliance can lead to severe fines, including fines and closures, further emphasizing the need for strenuous assessment protocols.
In addition, tank welding inspection plays an important duty in maintaining operational effectiveness. In summary, the relevance of tank welding assessment exists in its ability to protect public health and wellness, shield the environment, and make sure conformity with governing structures.
Key Evaluation Methods
Efficient storage tank welding assessment relies on a selection of vital techniques that ensure complete examination of weld top quality and architectural honesty. Amongst one of the most widespread techniques are visual inspection, ultrasonic screening, radiographic screening, and magnetic bit screening - Tank Welding Inspection. Each technique uses special benefits in analyzing various elements of the weld
Visual evaluation functions as the very first line of protection, permitting examiners to determine surface area problems, irregularities, or disparities in the weld bead. Ultrasonic testing employs high-frequency sound waves to detect interior defects, such as cracks or voids, giving a detailed assessment of weld honesty. This technique is especially efficient in discovering issues that might not be noticeable on the surface.
Radiographic testing uses X-rays or gamma rays to create pictures of the welds, revealing inner interruptions and giving a long-term record for future reference. This method is extremely reliable for important applications where the threat of failure have to be reduced.
Last but not least, magnetic bit screening is used to determine surface area and near-surface flaws in ferromagnetic products. By applying electromagnetic fields and great iron particles, assessors can pinpoint interruptions that might jeopardize the architectural stability of the tank. Together, these methods create a robust structure for making sure top quality welds in commercial applications.
Conformity With Safety And Security Standards
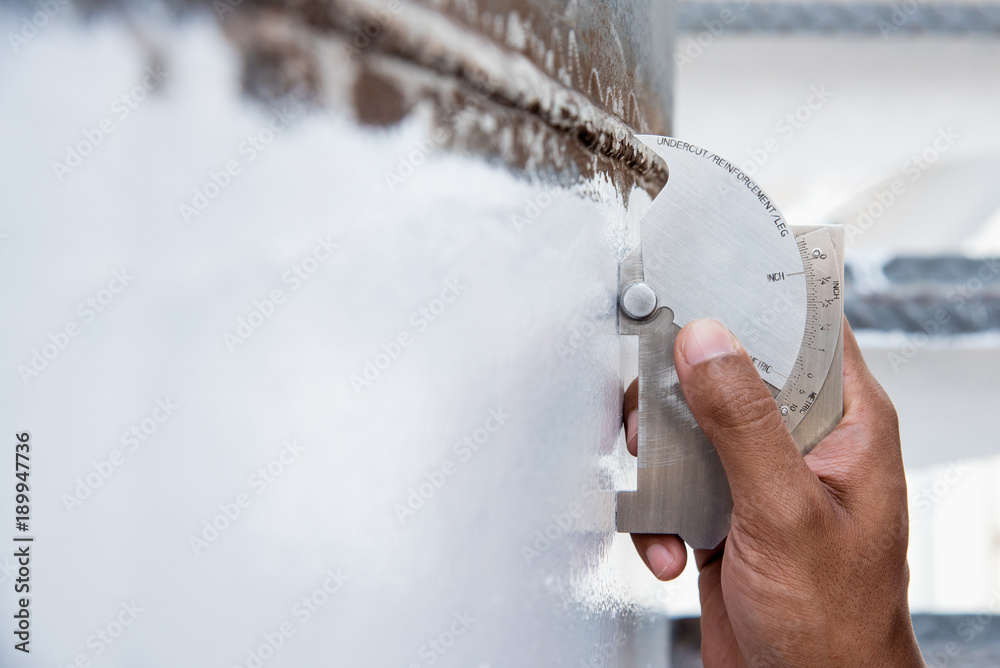
Regular inspections play a critical function in making sure conformity by determining prospective failures or variances from recommended requirements. Inspectors are trained to evaluate weld quality, validate product requirements, and evaluate the overall structural honesty of containers. Their know-how is essential in making sure that welding procedures satisfy the needed safety criteria.
Furthermore, conformity with security requirements not only safeguards workers yet additionally safeguards the atmosphere from potential hazards such as leaks or catastrophic failings. Organizations that focus on security compliance are much better positioned to alleviate risks, enhance functional effectiveness, and foster a society of security within their labor force. In recap, preserving rigorous conformity with security standards is essential for the effective operation of tank welding tasks in industrial setups.
Benefits of Normal Assessments
Regular assessments are essential to maintaining the architectural integrity and safety and security of welded tanks. These assessments provide an organized method to recognizing prospective issues or weaknesses in the welds, making certain that any type of concerns are attended to before they intensify right into considerable failings. By conducting normal assessments, companies can spot rust, fatigue, and other kinds of deterioration that might endanger tank efficiency.
In addition, regular evaluations add to conformity with industry guidelines and requirements. Adhering to these standards not just alleviates legal dangers however additionally enhances the organization's content track record for safety and security and integrity. Regular evaluations promote a proactive security society, urging staff members to recognize and prioritize the significance of equipment stability.

Study and Real-World Applications
Study and real-world applications illustrate the concrete influence of reliable storage tank welding inspection techniques. One remarkable instance is a huge petrochemical center that faced significant operational disturbances as a result of leakages in storage space containers. Complying with the application of extensive welding inspection methods, consisting of visual and ultrasonic screening, the facility recognized vital problems in weld joints that can have caused disastrous failures. This aggressive strategy not just prevented environmental risks yet likewise saved the company millions in possible clean-up costs and regulative fines.
Likewise, a water therapy plant executed a thorough evaluation program for its container welding operations - Tank Welding Inspection. By including non-destructive screening techniques, the plant had the ability to discover very early signs of rust and exhaustion in weld joints. This timely treatment expanded the lifespan of the storage tanks and made certain compliance with safety policies, thus protecting public wellness
These case research studies emphasize the significance of routine and organized storage tank welding assessments. By focusing on these techniques, industries can reduce visit here dangers, improve structural stability, and ensure conformity with safety requirements, eventually bring about boosted functional effectiveness and minimized liabilities.

Verdict
In conclusion, container welding evaluation is an indispensable element of maintaining architectural integrity and safety and security in industrial applications. Employing numerous evaluation techniques makes sure early discovery of potential imperfections, consequently preventing tragic failures.
Comments on “Exactly How Tank Welding Inspection Prevents Future Structural Failures”